3Dプリンターで設計物を出力する際に指定が必要なパラメータの一つに「レイヤー高さ」がある。 例えばレイヤー高さを0.3mmに設定していた場合、設計時に0.1mmの精度を期待して描いた図面でも出力物は0.3mm単位に丸められてしまう。どの厚さに丸められるかは、レイヤー高さを含め以下の要素にて決定されると言われている。
- レイヤー高さ
- (および初期レイヤー高さ)
- キャリブレーション時に調整するノズルとビルドプレートとの隙間とZオフセット
- キャリブレーション時の隙間と初期レイヤー高さ設定は厚みを相殺する関係にある
- ステッピングモーターのステップ角
- こちらは微細すぎるので考慮する人は少ない(が、考慮している人たちもいる)
丸めの単位は計算によって求められる雰囲気はあるが、キャリブレーション時の隙間のような数式組み込みが難しいパラメータも存在する。とりあえず手持ちのプリンターで印刷が良好に行えるキャリブレーション実施後の、初期レイヤー高さ0.2mm、レイヤー高さ0.3mmとしているときの厚み丸め状態を実物を観察することで把握してみることにした。
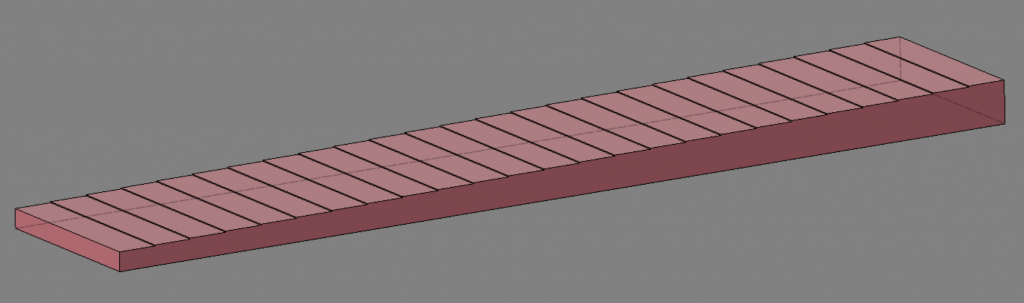
まずは上記のように、2mm厚から右に向かって0.1mmずつ25段階に厚みが増していくモデルを作図してスライスする。この時点で何段階に丸められるかは以下のようにわかる。ただ、最初の段(2.0mmのはず)についてもレイヤー高さ単位で丸められているはずなので、本当に2.0mmが出ているか、また右端の段が本当に4.4mmになっているかは印刷をしてみないとわからない。
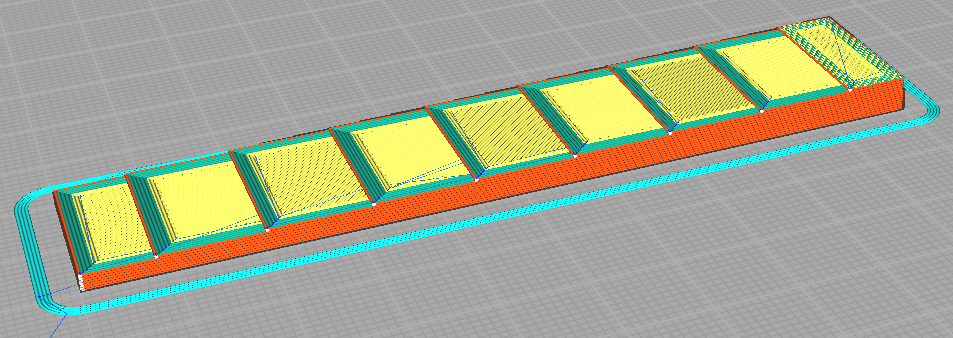
上記のスライスデータをプリントし、出力物にノギスを当てて測定した結果が以下の通りである。丸め後の段差は0.3mm単位で造成されているが、2.6mmの次が3.0mmとなり0.4mmの差があるなど、ずっと0.3mm単位の定量偏差があるわけではなさそうだ。この辺りを理解したい場合はモーターのステップ角なども考慮に組み込む必要が出てくるのだろうと思う。
上記のような特異段差がある状況下では、2.7mm厚で設計した部品と2.8mm厚で設計した部品はそれぞれ、2.6mm厚と3.0mm厚で出力されることになる。かたや薄くなり、他方は厚くなっている。これは危険だ。
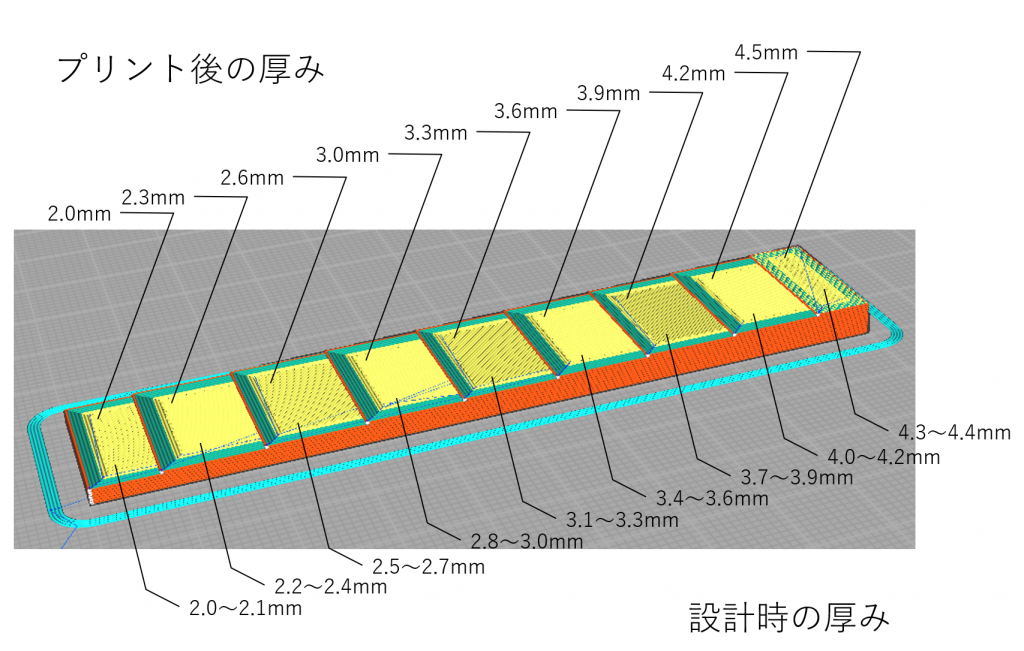
ここまで精度に着目して調べてきたが、「自分は0.1mm単位での設計はしていない。いつも1mm単位だ。」という人も気を付けなければならない。上の図でも明らかだが、2mmと3mmはそのままの厚さで出力できているが、4mmを出力しようとすると4.2mmになってしまうように、大きな単位で作図していても複数部品組み合わせ時のチリが合わなかったり、嵌め合いが失敗するなどの問題につながることがある。